What exactly is Six Sigma?
Six Sigma is a project-based approach for improving effectiveness and efficiency. It is a disciplined, customer-focused, data-driven approach for improving the performance of processes, products, or services.
It strives for a defect level that is no more than 3.4 parts per million(10 Lakh). Sigma is a letter in the Greek alphabet used to represent standard deviation, a measure of variation.
As a methodology, Six Sigma refers to the DMAIC, or D-M-A-I-C, a methodology for improvement, named after its five phases of define, measure, analyze, improve, and control.
In the define phase, the project is defined, the project team is selected, and management launches the Six Sigma project. The team is tasked with understanding what is important to customers and determine the performance outcome to be improved.
In Six Sigma, the performance outcome to be improved is known as the Y, as in Y is the function of x.
In the measure phase, the size and scope of the problem is understood and performance on Y is measured.
After we’ve defined and measured, we analyze. The data is analyzed to determine the causes of factors that impact performance. In other words, we diagnose and prove which X factors impact the Y.
Root cause analysis is performed so that the causes of full performance are determined.
Then, we move on to improve. In improve phase, solutions are developed to address the proven X factors so that Y can be improved.
Solutions are developed, piloted, and implemented to reduce the length and the variability of processing times.
Finally, we move on to control. In the control phase, controls are established to ensure that our improvements, or gains, are sustainable. Controls and procedures are put in place so that employees know when and how to intervene to ensure superior performance.
Key roles of executives and champions
Executives are the CEO and his or her direct reports, the C suite, the COO, the CFO, CIO, and so on and senior management such as vice presidents and directors. The role of executives and senior management is to deploy Six Sigma projects as a means to achieve the organization’s strategic and annual goals, establish project selection criteria, review and select projects, assign project champions, and review updates from champions, and provide resources as needed.
The project champion selects a project leader. The project leader is someone who plans, leads, and executes a project with the help of a designated project team. The project champion also approves the project charter. The project charter is a document that defines the project including its objectives, timeline, and scope. The champion provides time and resources for the project team to work on the project, and they reassign and redistribute work to others as needed. The champion receives updates from the project leader on a weekly basis.
Levels of expertise
Six Sigma is a discipline methodology for improvement. It is this discipline that was thought to be analogous to the strict discipline found in martial arts. So let’s explore the different belts, the type of training received, and their roles in the implementation of Six Sigma.
The white belt training introduces the basic concepts of Six Sigma including it’s quality concepts and process thinking. White belt training is knowledge based.
In yellow belt training the Six Sigma DMAIC methodology is introduced.
the concept of variation
voice-of-the-customer analysis
process mapping
brainstorming for root cause analysis.
Green belt training takes a participant through each phase of DMAIC, the steps involved and the corresponding tools used. Green belts are trained to lead and carry out DMAIC projects, usually on a part-time basis. The time commitment is about hours a week for the duration of the project.
In contrast, black belts are full-time Six Sigma specialists. These projects are broader in scope and more complex than a green belt project and they require advanced quality and statistical analysis. Black belts are trained in the advanced quality and statistical tools used in Six Sigma. These include for example process capability, inferential statistics, and design of experiments.
Master black belts are experienced black belts who have received additional training
advanced statistical analysis,
process simulation,
project management,
and change management.
Master black belts serve as Six Sigma trainers and coaches to the rest of the organization. Until they are developed, this role is outsourced to outside training and consulting firms.
Critical to quality metrics
These are what we call the Voice of the Customer, or VOC. VOC are needs and expectations expressed in the customer’s language.
Put another way, you have to translate the Voice of the Customer into Critical-to-Quality Requirements, or CTQs.
What are CTQs? CTQs are the performance characteristics of a process, product, or service, that are critically important to customers. CTQs are measurable in how good they need to be in order to satisfy the needs and expectations of customers, can be determined and established.
If you are managing a process, you benefit from learning about CTQs. With CTQs, you know what metrics to monitor and how well they must perform to satisfy customers. The underlying premise of Six Sigma projects is Y is a function of x.
Variation and the normal curve
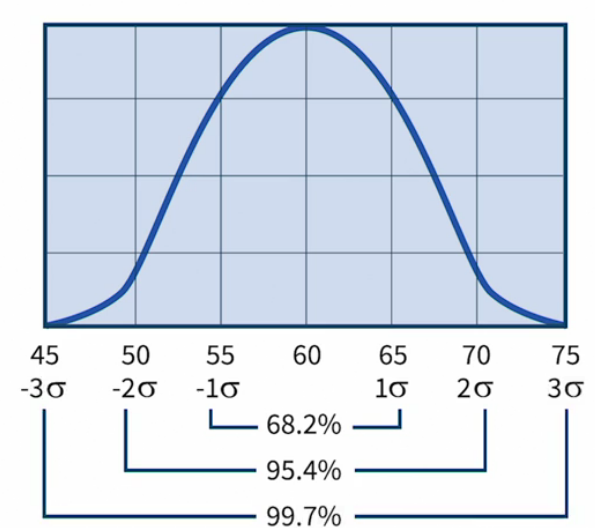
The variation is random. As you can see, this natural, random variation forms a bell-shaped curve. This bell-shaped curve is called the normal curve. All normal distribution. Your average or mean is in the middle, at 60 minutes. These percentages are universally true for all normal curves. There we have it, with the cost variation and the normal curve. Why is this important? Because as you learn more about Six Sigma, you will find that the normal curve is widely used to depict random variation in processes.
Discover more from My Tricky Notes
Subscribe to get the latest posts sent to your email.